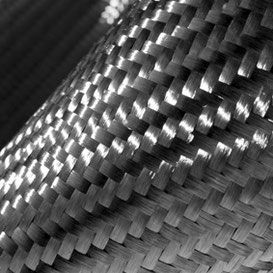
Seit der Einführung von Carbon in der Radsportszene Ende der 90er, Anfang der 2000er Jahre, hat die Fahrradindustrie die Grenzen der Machbarkeit zu immer leichteren, steiferen Bikekomponenten verschoben, sowie eindrückliche Formgebung und Designs eingeführt, welche mit herkömmlichen, metallischen Werkstoffen nicht möglich gewesen wären.
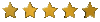
Trusted Service
Wo kommt das Rohmaterial, die Carbonfaser her
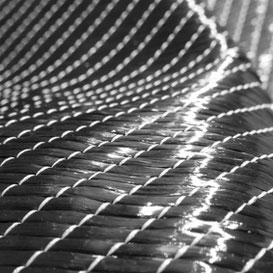
Carbonfasern werden auf der Basis organischer Ausgangsmaterialien gewonnen.
Die heute gebräuchlichen im Bikesport verwendeten CARBONFASERN sind HT (HighTenacity) und IM (Intermediate Modulus), darüberhinaus gibt es gängige Spezifikationen wie HM, UM, UHM, UMS und HMS (weitere Informationen im TECHNOLOGIECENTER). All diese Fasertypen werden aus Polyacrylnitril, kurz PAN genannt, durch Stabilisierungsreaktionen an der Luft und anschließend unter Schutzgas, einer Pyrolyse, hergestellt. Hierbei wird durch das Anlegen einer Zugspannung unter Schutzgasatmosphäre, sowie einer hohen Prozesstemperatur, ab ca. 1300°C, die Molekularstruktur so umgebaut, dass hohe mechanische Werte erzielt werden, wie Festigkeit, Steifigkeit und E-Modul, sprich Bruchdehnung.
Bei diesem Prozess werden alle übrigen Elemente vom Kohlenstoff gasförmig aus dem Verbund gelöst, mit steigender Temperatur nimmt somit die Reinheit auf 96-98% zu. Die eigentliche Carbonisierung / Graphitierung setzt oberhalb von 1800°C ein, hierbei werden die molekularen Strukturen für maximale mechanische Eigenschaften optimiert. Die Graphitierung wird bis ca. 3000°C durchgeführt, entsprechend hochwertiger und kostenintensiver ist dann das Rohmaterial.
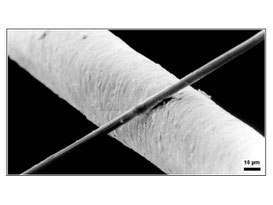
Die daraus gewonnene Carbonfaser, Fachbegriff Filament, hat typischer Weise einen Durchmesser von 6 µm, ein menschliches Haar liegt bei 50 µm ! Diese Filamente werden nun zu Bündeln, sogenannten Rovings von 1K bis 24K zusammengefasst, also Strängen, Rovings, von 1000 bis 24000 Einzelfilamenten (!). Diese Faserbündel wiederum werden dann zu unidirektionalen (UD) Bändern oder UD Gelegen vernäht, oder zu unterschiedlichen Gewebestrukturen wie Köper- / Atlas- oder Leinwandbindungen verwoben, man spricht nun von einem textilen Halbwerkzeug das zur Herstellung von Carbonbauteilen verarbeitet wird. Eine weitere Variante wäre die direkte Verarbeitung mit einem voll- oder halbautomatischen Wickelverfahren, Fachbegriff „filament winding“.
Der Herstellungsprozess der Carbonfilamente ist hoch technologisch und ausgeklügelt, weshalb es auch nur wenige Firmen dafür gibt. Mehr als 90% des Rohmaterials weltweit kommen von sechs Firmen: Cytec, Hexcel, Toray, Mitsubishi Rayon, Zoltek und Toray.
Rohstoff Carbon mit energetisch hoher Anfangshypothek
Ökologisch hat die Leichtbautechnik durch diesen energetisch intensiven Herstellungsprozess eine hohe Anfangshypothek. Ein Crashreplacement führt zu einer katastrophalen Ökobilanz, im Gegensatz zu einer Carbonreparatur.
Carbon als textiles Halbwerkzeug
Der gebräuchliche Ausdruck Carbon ist genau genommen nicht korrekt. Carbon als textiles Halbwerkzeug ist nur eine Komponente in Leichtbauteilen. Die exakte Beschreibung lautet: CFK - Carbon-Faserverstärkter Kunststoff. Das textile Halbwerkzeug muss durch eine sogenannte Matrix in Position gehalten, gebunden werden, um seine exzellente mechanischen Eigenschaften im Bauteil entfalten zu können, dem Epoxydharz. Das was gewöhnlich als Carbon bezeichnet wird, ist also ein Compositeverbund aus Faser und Harz. An dieser Stelle sei angemerkt, das dieser Aspekt ein Recycling erschwert, bzw. es nach aktuellem Stand der Technik zum einem Downcycling kommt, da die Faser als Ganzes nicht mehr aus dem Verbund gelöst werden kann, mechanisch geschreddert wird, oder durch chemische Prozesse zur Lösung der Matrix in ihren Eigenschaften reduziert wird.
Die Fahrradindustrie verwendet in der Fertigung überwiegend sogenannte Prepregs, also vorgetränkte Halbwerkzeuge, welche unter Raumtemperatur verarbeitet werden können und dann im Ofen unter Druck ausgehärtet werden.
Materialstandard und Eigenschaften werden nicht von der Fahrradindustrie bestimmt
Nahezu jeder Markenhersteller bewirbt seine Modelle mit Schlagwörtern wie z.B. Hightenacity (HT), Ultrahighmodulus (UHM) oder Highmodulus (HM) etc. Diese Begrifflichkeit stammt jedoch von der JCMA, der Japanese Carbon Fiber Manufacturers Association, basierend auf den mechanischen Eigenschaften der unterschiedlichen Fasertypen, wie Steifigkeit und E-Modul. Um mehr Alleinstellungsmerkmal und Aufmerksamkeit im Marketing zu bekommen kreieren einzelne Hersteller neue Slogans / Abkürzungen, die das Carbonfahrrad sprichwörtlich nicht neu erfinden und keine neue Materialtechnologie implementieren, sondern lediglich deren Anwendung / Verarbeitung in einem Carbonbike.
In Kürze folgt ein weiterer Blogartikel, wie die Carbonfaser spezifisch in der Konstruktion eingesetzt wird und wie das Leichtbaupotential ausgeschöpft werden kann.
Anfrage über unsere KONTAKT Seite.
Kommentar schreiben